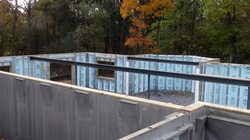
Another busy day at the home site! The crane was gone and three new steel beams were installed. The largest of the three beams runs the entire width of the entire house. The second is across the great room and the third across our master bathroom. These beams support the joists that in turn support the sub floor (these three elements make up the ‘plate’). In addition to the beams the main drain lines were installed and more grading was done for the RV garage which will be located at the northern edge of the property.
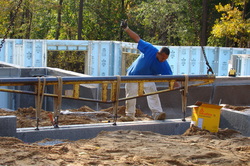
By the time we got to the site at lunch time on Monday, the Superior Wall wizards were once again there and gone. This time they delivered and installed the garage footings. The installers were again measuring and doing the final adjustments. We noticed that wood boards were being laid all along the top of the foundation walls. Not sure why but we believe it is in preparation for installing the plate. Dan M. met us at the site to discuss his suggestion that we add provisions for water and sewer at the lower level even though we won’t be finishing the basement. The logic is that it is much easier and cost effective to do this now before the cement floor is poured rather than in the future. So after much discussion (and cost analysis!) we decided to go ahead with their suggestion – another change order!
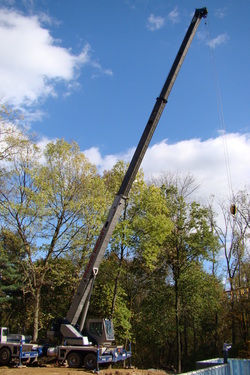
By the time Ralph got to the house around 10:30 am, gravel trucks were there and gone. They dumped enough stone to fill the basement floor, completely covering the cement footers. This stone plays a critical role in providing support to the Superior walls which were sitting on two large flat bed trucks. The first truck had already backed down the makeshift driveway, waiting to be unloaded. As Ralph walked towards the truck he couldn’t miss the huge crane firmly rooted to the ground close to the front of the house. A word about Superior Walls… They are manufactured concrete basement wall sections reinforced with rebar, insulated and ready to have wall board installed on the interior walls. They are made of high pressure concrete and require no additional water proofing. Each piece is precisely measured and constructed to the builder’s specifications, ready to be lowered into place by one very talented crane operator. As you will see in the pictures, the walls are manufactured with openings for the two doors and one window specified in the plans for our walk out basement. Once in place, the wall pieces are bolted together and sealed. Superior Walls were invented in Lancaster by a local builder in 1981 and are now distributed in 25 states. (end of commercial!).
Ralph went home eager to tell me all about his adventures and we made immediate plans to go back together to watch the walls be hoisted into place. We made it back to the house by 3:00 and, much to our surprise, every single wall was in place and the trucks were gone! The two installers were carefully measuring the position of each wall and on several occasions used the crane and the lift to adjust individual sections. We were disappointed to miss the flying walls but thrilled to be able to walk around in what now really felt like a basement! Everything seemed so much bigger once the walls were in place.

Once again we went down to the house at lunch time. Boy, do these people work fast! The basement was completely excavated and cement pads or “footers” were framed and filled with cement. These footers are four foot by four foot cement pads (one foot deep!) that will support steel posts. These posts which reach up and through the first floor ‘plate” are what the wood posts will then rest on. Rather than just placing the wood posts directly on the plate or on the perimeter of the foundation, this method provides a much more rigid and secure support system. Remember, in post and beam construction, it is the wood frame that supports the entire structure, not the walls which provide the support in regular ‘stick’ construction. They also added an additional cement pad for extra support for the staircase.
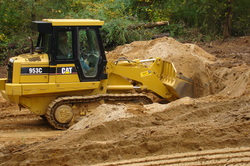
Dan M. said the crew got to our site later in the day on Monday which seems a bit strange since we were there around 3:00. But, today is the day! At lunch time we made a bee line to Strasburg and this time we found lots of activity! The narrow path (our future driveway!) was widened and two large piles of stone were laid down to provide a more solid foundation for the heavy equipment. The top soil had already been scraped off and was piled high in a big mound out of the way. A front end loader was busy scooping out dirt and distributing it to various parts of the property. We could actually see the beginning of the basement! A backhoe was digging out more of the driveway and doing some grading. We later realized this was to create access for the flatbed trucks that would be delivering the Superior walls for the foundation. To the untrained eye (mine) it look an awful lot like two grown men playing with their Tonka toys in the dirt!
Our project manager, Ken, was on site so we had the opportunity to introduce ourselves and talk to him about the plans for the rest of the week. We were mesmerized watching the process unfold. Finally, it was beginning to seem real. As much as we wanted to stay and keep watching, it was time to go back to work. We all but bounced back to the car, grinning from ear to ear! What a rush!
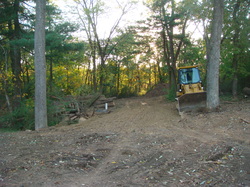
The one advantage of our trip being cut short is being able to see the builder break ground. We were resigned to missing this moment so we were really excited! Finally, after all these months of planing and talking, Today is the day we would actually have a hole in the ground! After unpacking the RV and taking it back to Mt. Joy, we hurried down to Strasburg full of anticipation. But, alas, disappointment one more time! There was not a woker to be seen and the one piece of construction equipemnt was just sitting there looking lonely! Time to call Dan M. to find out about the delay!
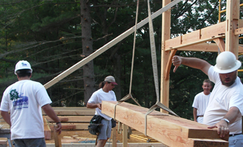
Each time we visited a Riverbend home the owners encouraged us to make a trip to Riverbend to watch the production of our timbers. With Dan T.'s help we scheduled our visit to coincide with the manufacture of our timber which (finally) was scheduled to begin on Monday, October 11th. The process takes a little over a week so we planned our visit for Monday, October 18th. Since the trip was about 493 miles we decided to include a stop in Pittsburgh to visit Lauren. We packed up our RV and headed to Pittsburgh on Thursday, October 14th excited to see Lauren and our 'wood'!
We had a great visit with Lauren until my phone rang on Saturday morning. Riverbend's General Manager was calling to tell us they had had an extensive fire in their production area early that morning. Fortunately, no one was hurt AND our wood safe! Dan later told us if the fire had been one day later our timber would have been moved to the area that was destroyed. Whew, what a relief! Needless to say our trip to Michigan was off. On Sunday we packed up the RV and headed home, disappointed and unsure if we would have the opportunity to reschedule our visit.
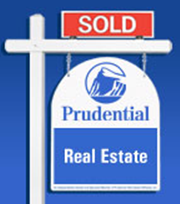
Unlike buying a house where you sign a lot of papers, get a couple of sets of keys and hurry back to a moving truck, we signed a LOT of papers and went back to work with a pen! What we really got was the promise of a house in the form of a construction loan. The process of applying for and getting approval for this type of a loan was quite the lengthy experience, to say the least. We filled out the mountain of paperwork in early August and then went through an unbelievable "interrogation" of our finances, credit history, work history and anything else the mortgage company decided to ask for. I think it would have been easier to give them our second born even though we only have one child!
After providing months of bank statements and years of our tax returns (personal and business) the staw that broke the camel's back was when the bank asked for copies of our check stubs. Now, think about that ... who do we work for? As I said to the bank officer: "I can make a check stub say anything you want!" With all the documents we had already provided they had more than enough proof of out income. We put our foot down and simply refused! Enough is enough!
Construction loans are difficult to begin with because money is being loaned for something that doesn't even exist. I get it. What this means is the mortgage company relys on three things: 1) An appraisal, 2) Comparables, and 3) the building plans and cost estimate provided by the builder. With out going into too much detail let me just say that it took more than 3 weeks just to find someone to do an appraisal, there are no comparables because there are no timberframe homes that are on the market or have sold in the last two years within a 70 miles radius and lastly, the building plans really didn't mean much because they are, at that point, mostly theoretical. We were horrified when the appraisal came in at less than half of the value of the land and the builder's estimate. Add that to the current problems with the economy that make borrowing money next to impossible and we were seriously wondering if we were going to get the construction loan. We were beginning to think we would be living in a tent in Strasburg. But after dotting our i's and crossing our t's, two months later we finally got the approval. What a relief!
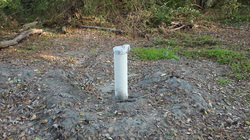
Since there is no public water or sewer on our property (a first for both of us!) the first step is to have a well drilled. Although the ground was "perked" before we bought it, our Township (Strasburg) requires that a well be drilled before the builder can even apply for any required permits.
When I think of a well I think of Timmy and Lassie ("Lassie, go get Ma, Timmy has fallen down the well"!!). But pictured here is our well! And the good news is that we hit water at 200 feet and there is more than enough - 30 gallons per minute.
Hmm... I'm hoping this big ugly pipe won't be sticking up in the middle of our front yard!
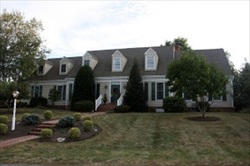
On the day we listed our house the local newspaper announced that recent home sales in Lancaster County were the lowest of all time. What, are we completely nuts?? Well, somewhat. But after all, we started this process 18 months ago with the belief that by the time we were ready to put our house on the market the economy would be on the upswing. So much for that logic! After months of sorting through every closet, drawer and cabinet, a yard sale in 90+ temps, numerous trips to Goodwill and a thorough top to bottom house cleaning, we were ready! On the advice of many articles on "staging", I put away our knick knacks, took down all the family pictures, hid our toothbrushes and paper towel holder and poof - the house looks like a model home and almost sterile. Nobody lives this way but it's a game we have to play - by taking everything that represents "us" it makes it easier for the prospective buyer to see themselves living in this house. I have to admit, it does make the house look bigger and I am enjoying how neat and organized everything is. However, I know I won't enjoy trying to keep it this way! Now we wait for the phone to ring!