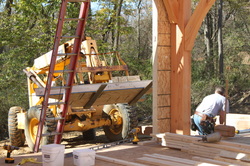
The day started off as a puzzle - looking at the SIP plans, deciding where to start and then searching through the piles of panels to find all the right ones (just like building Legos!) Once again the Traverse proved invaluable to move the panels from the street up to the building site. But, as you will see in the pictures, sometimes it's just faster to grab a panel and throw it over your shoulder. Which is exactly what Art did when he realized they had pulled a wrong panel!
The task didn't get any easier when another flat bed truck loaded with more SIPs showed up around 11:30. The puzzle work stopped for the crew to once again unload the panels. The front of our house was beginning to look like the Insulspan factory we had seen weeks before!
We were fascinated by the variety and size of the SIPs. Some of the panels were huge (for the roof?), some were so small (see Ralph holding one of these) and some had extra reinforcement with LVL (laminated veneer lumber).
More about SIPS (skip this part if you don't want to read the technical details!!) As I mentioned before, the Insulspan Structural Insulating Panels are “sandwiches” of performance-rated oriented strand board (OSB) structurally laminated to a continuous core of expanded polystyrene (EPS) insulation. For our house our wall 'sandwiches' are 6.5 inches thick and 10.5 inches for the roof. SIP construction is very popular with timber frame construction because the timbers, not a wood frame, support the house. Using the pre-made SIP's reduces construction time and improves energy efficiency. Once complete, we will have R values of 23 for the walls and 40 for the roof. In addition to the increased R value, SIP construction prevents air movement caused by gaps around wood framing and by settling of insulation. The continuous core of EPS insulation in SIPs reduces air leakage and heat loss, while allowing better control of indoor air quality. All windows and most door openings (not our front door) are pre-cut at the factory, further simplifying the construction process.
To install a panel, 2x6's are first nailed along the edge of the plate. The 2x6 is lined with a special sealant/adhesive designed to seal off gaps and act as an adhesive. The SIP is raised and put in place over the 2x6 (the OSB board extends beyond the polystyrene on both sides so it fits snuggly over the 2x6). The panel is connected to an adjacent panel or to the frame with very long screws - 8 and 10 inches long. At the bottom, just above the plate, the OSB is nailed to the 2x6. Two part expanding foam is injected into certain joints and any gaps or voids, as needed.
Once the crew installed a few fairly simple panels, Art decided to tackle the SIPs for the bay window, a far more complex installation. Since this was Art's last day on site, he wanted to give Barry as much exposure to as many types of installations as possible. Barry and Art finished the day by going over the SIP plans in great detail and discussing the plan for the rest of the installation. It was Art's feeling that the entire structure would be enclosed within three weeks, providing the weather cooperated!
We said our thanks and good-byes to Art and headed home. Watching the SIPs being installed was very interesting but in a strange way it almost seemed a shame to enclose the frame. But, living there without benefit of the walls and insulation wouldn't work either!!
The task didn't get any easier when another flat bed truck loaded with more SIPs showed up around 11:30. The puzzle work stopped for the crew to once again unload the panels. The front of our house was beginning to look like the Insulspan factory we had seen weeks before!
We were fascinated by the variety and size of the SIPs. Some of the panels were huge (for the roof?), some were so small (see Ralph holding one of these) and some had extra reinforcement with LVL (laminated veneer lumber).
More about SIPS (skip this part if you don't want to read the technical details!!) As I mentioned before, the Insulspan Structural Insulating Panels are “sandwiches” of performance-rated oriented strand board (OSB) structurally laminated to a continuous core of expanded polystyrene (EPS) insulation. For our house our wall 'sandwiches' are 6.5 inches thick and 10.5 inches for the roof. SIP construction is very popular with timber frame construction because the timbers, not a wood frame, support the house. Using the pre-made SIP's reduces construction time and improves energy efficiency. Once complete, we will have R values of 23 for the walls and 40 for the roof. In addition to the increased R value, SIP construction prevents air movement caused by gaps around wood framing and by settling of insulation. The continuous core of EPS insulation in SIPs reduces air leakage and heat loss, while allowing better control of indoor air quality. All windows and most door openings (not our front door) are pre-cut at the factory, further simplifying the construction process.
To install a panel, 2x6's are first nailed along the edge of the plate. The 2x6 is lined with a special sealant/adhesive designed to seal off gaps and act as an adhesive. The SIP is raised and put in place over the 2x6 (the OSB board extends beyond the polystyrene on both sides so it fits snuggly over the 2x6). The panel is connected to an adjacent panel or to the frame with very long screws - 8 and 10 inches long. At the bottom, just above the plate, the OSB is nailed to the 2x6. Two part expanding foam is injected into certain joints and any gaps or voids, as needed.
Once the crew installed a few fairly simple panels, Art decided to tackle the SIPs for the bay window, a far more complex installation. Since this was Art's last day on site, he wanted to give Barry as much exposure to as many types of installations as possible. Barry and Art finished the day by going over the SIP plans in great detail and discussing the plan for the rest of the installation. It was Art's feeling that the entire structure would be enclosed within three weeks, providing the weather cooperated!
We said our thanks and good-byes to Art and headed home. Watching the SIPs being installed was very interesting but in a strange way it almost seemed a shame to enclose the frame. But, living there without benefit of the walls and insulation wouldn't work either!!