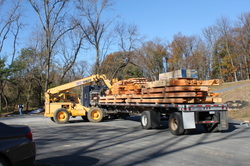
Although I'm not a pessimist by nature, on the drive to Strasburg I was all but convinced that something had gone wrong and the truck wouldn't be there. Fortunately, I was wrong! We got to the site at 9:30 and the truck was there and almost halfway unloaded. Barry was moving the wood with a piece of equipment called a Traverse (looks like an overhead fork lift to me). He was zipping around the property carefully creating stacks and stacks of wood. Timbers of all sizes and shapes were everywhere! He looked like he was having much too much fun! He really showed off his skills as he carried four pieces of wood that were wider than the driveway and extended beyond both of the flanking trees. I held my breath! The last piece of wood to come off the truck is called an architectural glulam. A glulam is 16 2 x 6 boards that are stacked on top of each other and glued together, forming a beam. The glulam will provide support in the ridge of the garage which is made of only SIPS with no timber support. This engineered beam is requird because the span is 33 feet long, much too great for a single piece of wood.
Once the wood was unloaded and sorted it was time to grab a quick lunch and wait for the crane to show up. While we were at lunch Art, our advisor from Riverbend, discovered that one of the posts was cut incorrectly. Maybe my worries of the morning were coming to fruition! Unfortunately, it was one of the larger posts and to have it re-made would delay the raising for a minimum of three weeks. Not good. Art made numerous calls to the designers and engineers in Blissfield as they poured over the plans, discussing alternatives. He finally called us over to explain the situation and the proposed solution. The first time he explained it I was convinced he was speaking Greek. Even Ralph didn't understand! Reading the architectural plans with our untrained eyes was no easy task. Seeing the glazed look in our eyes, Art had a great idea: he used a visual aid! He inserted a small beam from one of the piles into a post on the ground to demonstrate the problem. Ahhh, the light bulb went on! He assured us that, visually, it would take a protractor to tell the difference and that they would only need to make a couple of replacement braces to accomodate the change. The braces would be delivered with the SIPs on Thursday. Problem solved!
When Art first discovered the problem he immediately put a hold on the crane. Crane time is expensive and the last thing anyone wants is a crane sitting idol. But the day was not lost as there was plenty of work to be done assemblying the bents. Fortunately, the Traverse can handle a lot of the "lifting" at lower heights - perfect for moving the heavier pieces of wood into position. As we watched, the first bent was assembled. Steel plates were inserted at the main joints to provide support and a very long threaded rod was inserted at the peak. Large metal pegs were pounded into the wood through the metal plates. All of the other joints were joined with oak pins. I was amazed at what a finished look the oak pins gave the bent. Speaking of being amazed, we were both completely blown away by the size and the beauty of the wood. Some of the knots in the wood almost looked like art work!
After the first bent was completed they started on the second bent that they actually assembled on top of the first bent. This puts both bents in position to be lifted, one at a time, by the crane and positioned on the steel beams, through the plate.
After the first bent was finished it was time to head back to Lancaster and check in with the office. We didn't do anything strenuous but all the fresh air and excitement left us exhausted and eager for tomorrow!
Once the wood was unloaded and sorted it was time to grab a quick lunch and wait for the crane to show up. While we were at lunch Art, our advisor from Riverbend, discovered that one of the posts was cut incorrectly. Maybe my worries of the morning were coming to fruition! Unfortunately, it was one of the larger posts and to have it re-made would delay the raising for a minimum of three weeks. Not good. Art made numerous calls to the designers and engineers in Blissfield as they poured over the plans, discussing alternatives. He finally called us over to explain the situation and the proposed solution. The first time he explained it I was convinced he was speaking Greek. Even Ralph didn't understand! Reading the architectural plans with our untrained eyes was no easy task. Seeing the glazed look in our eyes, Art had a great idea: he used a visual aid! He inserted a small beam from one of the piles into a post on the ground to demonstrate the problem. Ahhh, the light bulb went on! He assured us that, visually, it would take a protractor to tell the difference and that they would only need to make a couple of replacement braces to accomodate the change. The braces would be delivered with the SIPs on Thursday. Problem solved!
When Art first discovered the problem he immediately put a hold on the crane. Crane time is expensive and the last thing anyone wants is a crane sitting idol. But the day was not lost as there was plenty of work to be done assemblying the bents. Fortunately, the Traverse can handle a lot of the "lifting" at lower heights - perfect for moving the heavier pieces of wood into position. As we watched, the first bent was assembled. Steel plates were inserted at the main joints to provide support and a very long threaded rod was inserted at the peak. Large metal pegs were pounded into the wood through the metal plates. All of the other joints were joined with oak pins. I was amazed at what a finished look the oak pins gave the bent. Speaking of being amazed, we were both completely blown away by the size and the beauty of the wood. Some of the knots in the wood almost looked like art work!
After the first bent was completed they started on the second bent that they actually assembled on top of the first bent. This puts both bents in position to be lifted, one at a time, by the crane and positioned on the steel beams, through the plate.
After the first bent was finished it was time to head back to Lancaster and check in with the office. We didn't do anything strenuous but all the fresh air and excitement left us exhausted and eager for tomorrow!