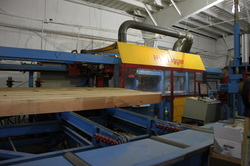
This was truly a once in a life time day! Promptly at 9:30 am, cameras in hand, we met Luke (Production Manager), Tom (Logistics Supervisor) and Bruce (Eastern Region Sales Manager and our tour guide for the day!) at Riverbend's production office. Ralph helped Tom locate our house (it's not on any maps yet) and then we donned our high fashion safety glasses and made our way out to the production area. Riverbend is really two plants: 1) Riverbend Timber Frame which creates the actual timbers and 2) Insulspan which creates the SIPS (Structural Insulated Panels). The two production facilities are in separate buildings, joined by a dust collection system. As a result of this separation the Insulspan Plant was unaffected by the recent fire except for some minor electrical disruptions which were fully restored during the weekend of the fire.
We started our tour on the Riverbend side and were introduced to the machine you see above, known as the Hundegger K2. It is a computer aided cutting machine that picks up a timber and moves in into position in the cutting bay. Then, based on the program for that piece, it cuts the timber to the specified size, cuts any angles, cuts out the mortises (male ends) or tenons (female ends), drills holes for the pegs, or any other necessary cuttings. The machine moves the timber along a track as the cutting tools move into position to make the very precision cuts. The cutting devices (knives, saws, blades) are very sharp and are typically sharpened every day. The entire machine is also calibrated daily. Once all the cuts are made, the machine moves the timber out of the bay and down the steel track to be inspected (by a human!) and removed from the platform by a fork lift. It is then brought out to the production floor and a special wax based sealant is applied to open grain wood such as Timber ends and mortises. Ralph and I were mesmerized by the whole process and had difficulty grasping that these were the posts and beams that would be holding up our house!
In some cases additional cutting that can't be done by the K2 machine is done by hand. Examples would be cutting an arch in a brace, carving a date or cutting more complex joinery.
Once the timbers are cut they are assembled on the shop floor to properly pre-fit the joinery, square the bents, and drill the oak pins. This process insures that installation at the building site can be done quickly and accurately and eliminates on-site cutting or adjustments. Once the timbers are properly fit, all the parts are disassembled and stacked by number (each piece is numbered according to the plan and hand initialed by the person who cut it!).
After this process, the timber is then put through another machine, the HM4, which planes the wood and adds any specified chamfers (cuts on the vertical edges for design purposes). The planing process smoothes out the wood and removes any markings or damage to the surface of the wood.
The final step, which we did not see, is the application of an oil that is designed specifically for unseasoned stock. "Green" or "unseasoned" timbers still have to dry after finishing. The finish is designed to breath, allowing moisture to pass through without causing damage. This method of oiling timbers gives the wood a finished look without hampering the seasoning process.
Bruce had to all but drag us away from the K2 so we could move on to the Insulspan operation. This is where the SIPS (Structural Insulated Panels) are manufactured. All though SIPS aren't quite as exciting as timbers, they are an important part of the timber frame building process. SIP's are comprised of oriented strandboards (OSB) that are held like the wafers of a sandwich by the inner layer Expanded Polystyene, which is the insulating core. With this design, SIPs have superior insulating qualities and produce a super tight building envelope or shell. The SIPS will be used both for our exterior walls and the roof of our house and the RV garage. Each SIP is computer designed to be cut specifically to our house plan and to integrate with the timbers. All of the openings for windows and doors are pre-cut, again to insure accuracy and ease of installation at our home site.
Both Ralph and I love to see how things are made so we really enjoyed watching the OSB and Polystryene "sandwiches" being made and cut. On our way out, Bruce showed us the machine that creates the "wire chases" through the polystyrene to accommodate the wiring in the house.
Bruce took us back to the Riverbend side where they were pre-assembling a bent (a bent is the combination of posts and beams, typically spanning a specific area). As we soon learned, this was the bent that will support our front porch. This moment was the pinnacle of our trip to Michigan - it made the wait and the trip so worthwhile! After looking at plans for so many months and even looking at the foundation back in Strasburg, this was reality. Here, in front of our very eyes, was the wood that would span the 30 feet of our front porch. It looked so big and the wood was so beautiful. It actually brought tears to my eyes as, at that moment, I realized this represented the reality of my dream of a timber frame home. After all the planning and worrying, I could finally see and touch the real thing. And this was just what was outside - I could only imagine what will be inside!!
After taking many, many pictures, Bruce dragged us away and reluctantly we returned our protective eye wear as we left the building! We hopped in our car and followed Bruce to the other end of town to Riverbend's Corporate and design office. We toured the offices and spent some time talking with Marty Birkenkamp, Design Manager and Chuck Meyer, Vice President. We were impressed with the caliber of every employee we met, at every level. Everyone was enthusiastic about their work, interested in us as customers and seemed very contentious about their jobs.
After our tour, Bruce took us back to town (population 2300!) and treated us to a delightful lunch at The Stable. He told us a great story about Marty on the night of the fire: At 2:00 in the morning, as the fire raged on, Marty was on the scene chasing after the Firemen yelling "I have a key, I have a key", trying to prevent them from chopping away at the building with their big axes!
After lunch, at my request, we made one more quick visit to the Riverbend facility in hopes that we might see another bent being assembled. Sadly, nothing was on the floor, but we did get to see two of the largest timbers that will be in our house -32 feet long. And that's 32 feet in one continuous piece - imagine the size of the tree that came from!
Although we both hated to leave, it was time to get on the road home. With 510 miles to cover we were already leaving later than we had planned - 1:45 pm. We thanked Bruce profusely and left Blissfield, grinning from ear to ear. We were exhausted from the excitement but couldn't stop talking about our experience. We made it home by 10:45, totally exhausted. But what a day it was!
We started our tour on the Riverbend side and were introduced to the machine you see above, known as the Hundegger K2. It is a computer aided cutting machine that picks up a timber and moves in into position in the cutting bay. Then, based on the program for that piece, it cuts the timber to the specified size, cuts any angles, cuts out the mortises (male ends) or tenons (female ends), drills holes for the pegs, or any other necessary cuttings. The machine moves the timber along a track as the cutting tools move into position to make the very precision cuts. The cutting devices (knives, saws, blades) are very sharp and are typically sharpened every day. The entire machine is also calibrated daily. Once all the cuts are made, the machine moves the timber out of the bay and down the steel track to be inspected (by a human!) and removed from the platform by a fork lift. It is then brought out to the production floor and a special wax based sealant is applied to open grain wood such as Timber ends and mortises. Ralph and I were mesmerized by the whole process and had difficulty grasping that these were the posts and beams that would be holding up our house!
In some cases additional cutting that can't be done by the K2 machine is done by hand. Examples would be cutting an arch in a brace, carving a date or cutting more complex joinery.
Once the timbers are cut they are assembled on the shop floor to properly pre-fit the joinery, square the bents, and drill the oak pins. This process insures that installation at the building site can be done quickly and accurately and eliminates on-site cutting or adjustments. Once the timbers are properly fit, all the parts are disassembled and stacked by number (each piece is numbered according to the plan and hand initialed by the person who cut it!).
After this process, the timber is then put through another machine, the HM4, which planes the wood and adds any specified chamfers (cuts on the vertical edges for design purposes). The planing process smoothes out the wood and removes any markings or damage to the surface of the wood.
The final step, which we did not see, is the application of an oil that is designed specifically for unseasoned stock. "Green" or "unseasoned" timbers still have to dry after finishing. The finish is designed to breath, allowing moisture to pass through without causing damage. This method of oiling timbers gives the wood a finished look without hampering the seasoning process.
Bruce had to all but drag us away from the K2 so we could move on to the Insulspan operation. This is where the SIPS (Structural Insulated Panels) are manufactured. All though SIPS aren't quite as exciting as timbers, they are an important part of the timber frame building process. SIP's are comprised of oriented strandboards (OSB) that are held like the wafers of a sandwich by the inner layer Expanded Polystyene, which is the insulating core. With this design, SIPs have superior insulating qualities and produce a super tight building envelope or shell. The SIPS will be used both for our exterior walls and the roof of our house and the RV garage. Each SIP is computer designed to be cut specifically to our house plan and to integrate with the timbers. All of the openings for windows and doors are pre-cut, again to insure accuracy and ease of installation at our home site.
Both Ralph and I love to see how things are made so we really enjoyed watching the OSB and Polystryene "sandwiches" being made and cut. On our way out, Bruce showed us the machine that creates the "wire chases" through the polystyrene to accommodate the wiring in the house.
Bruce took us back to the Riverbend side where they were pre-assembling a bent (a bent is the combination of posts and beams, typically spanning a specific area). As we soon learned, this was the bent that will support our front porch. This moment was the pinnacle of our trip to Michigan - it made the wait and the trip so worthwhile! After looking at plans for so many months and even looking at the foundation back in Strasburg, this was reality. Here, in front of our very eyes, was the wood that would span the 30 feet of our front porch. It looked so big and the wood was so beautiful. It actually brought tears to my eyes as, at that moment, I realized this represented the reality of my dream of a timber frame home. After all the planning and worrying, I could finally see and touch the real thing. And this was just what was outside - I could only imagine what will be inside!!
After taking many, many pictures, Bruce dragged us away and reluctantly we returned our protective eye wear as we left the building! We hopped in our car and followed Bruce to the other end of town to Riverbend's Corporate and design office. We toured the offices and spent some time talking with Marty Birkenkamp, Design Manager and Chuck Meyer, Vice President. We were impressed with the caliber of every employee we met, at every level. Everyone was enthusiastic about their work, interested in us as customers and seemed very contentious about their jobs.
After our tour, Bruce took us back to town (population 2300!) and treated us to a delightful lunch at The Stable. He told us a great story about Marty on the night of the fire: At 2:00 in the morning, as the fire raged on, Marty was on the scene chasing after the Firemen yelling "I have a key, I have a key", trying to prevent them from chopping away at the building with their big axes!
After lunch, at my request, we made one more quick visit to the Riverbend facility in hopes that we might see another bent being assembled. Sadly, nothing was on the floor, but we did get to see two of the largest timbers that will be in our house -32 feet long. And that's 32 feet in one continuous piece - imagine the size of the tree that came from!
Although we both hated to leave, it was time to get on the road home. With 510 miles to cover we were already leaving later than we had planned - 1:45 pm. We thanked Bruce profusely and left Blissfield, grinning from ear to ear. We were exhausted from the excitement but couldn't stop talking about our experience. We made it home by 10:45, totally exhausted. But what a day it was!